Last Monday, I did something that I said I wouldn’t do. I bought a floor loom after promising my husband (and myself) that I did not need one and wouldn’t buy another one. And, normally, I would’ve kept that promise.
But when my neighbor up the road (the same one who helps shear my sheep) decided to sell her floor loom, I couldn’t resist. It was a great price and it was three minutes up the road. (If you’ve ever transported a floor loom, you understand the significance of one being that close by.) We were able to load the loom onto the back of a truck without taking it apart, covering it with a tarp, or even strapping it down. (The first floor loom I bought had to be disassembled before it even left the seller’s house because it wouldn’t fit through the front door). Had the loom been 30 minutes away, I would have turned it down.
This particular loom—a 1974 Nilus Leclerc (4 shaft, 46” weaving width)—had been bought in Franklin, TN in 2022 and transported to North Alabama by my neighbor who decided that she didn’t have time to learn how to set up a floor loom after all. This happens frequently with hopeful weavers. It hadn’t been used in a while and the tie-up pins were missing, so it had been sitting in my neighbor’s garage for the past year collecting dust.
The night before picking up the loom, I decided to do some research—not only on this particular loom model, but also on an easier method of warping. My last floor loom had a sectional beam, but this one did not. Being used to direct warping a rigid heddle, I’m spoiled on quick, easy loom dressing. So, naturally, I hopped on YouTube to see if anyone had attempted direct warping a floor loom. I found three videos.
So, as soon as the loom was in place in my bedroom corner and I had improvised some tie-ups for the treadles, I got to work direct warping the loom. I used some of the cotton cone yarn that came with the loom (super old pearl cotton) instead of my own yarn—just in case this method didn’t work for me. But, it worked, so after I use up this warp, getting the feel for a floor loom again, I’ll set up a wool warp for the next round.
*Direct warping will not work for every weaving project on a floor loom, especially if you’re using extremely fine threads (which I don’t plan to be using).
For those interested in direct warping a floor or table loom, here are the two most useful videos I found.
I finished two scarves last week—one with some cotton/silk/linen yarn from my stash—and another tartan scarf: Black Watch Military. I’m up to 7 tartan scarves so far and with about 5 weeks to go, I’m guessing I’ll have about 13 or so total tartan scarves for the festival. I’ll be taking custom tartan orders on the day of the festival, however, for anyone who wants one that I don’t currently have worked up.
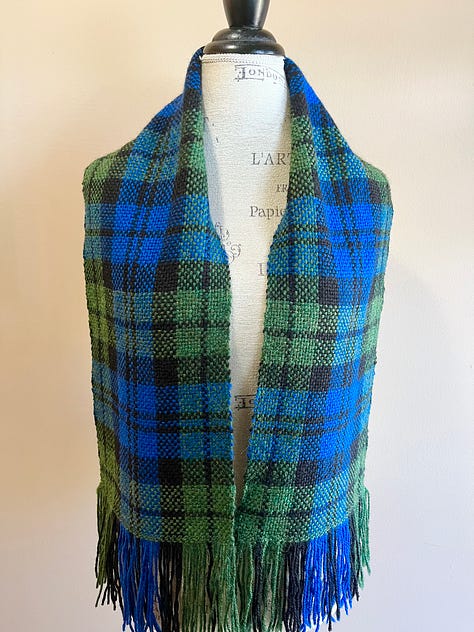
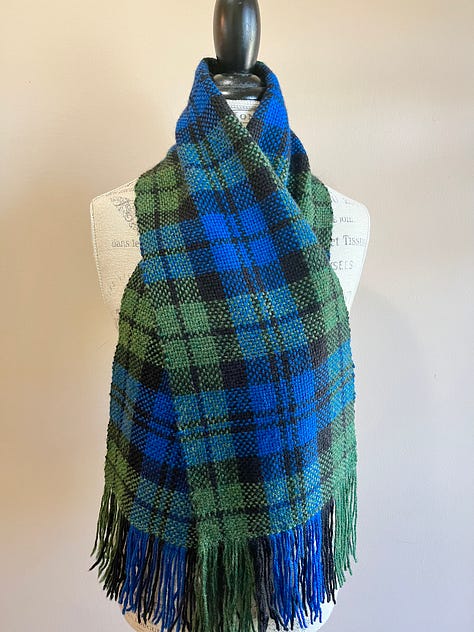
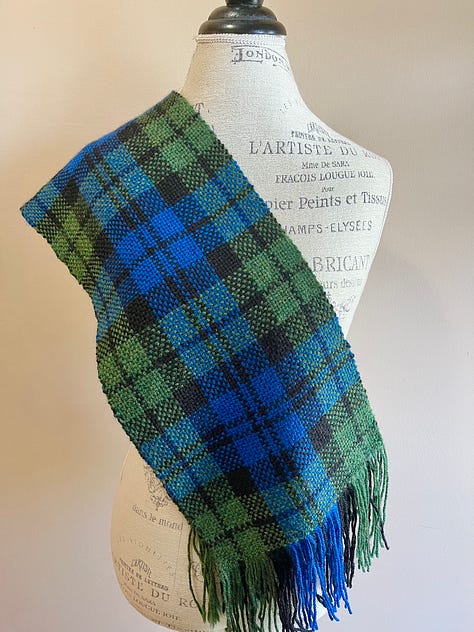
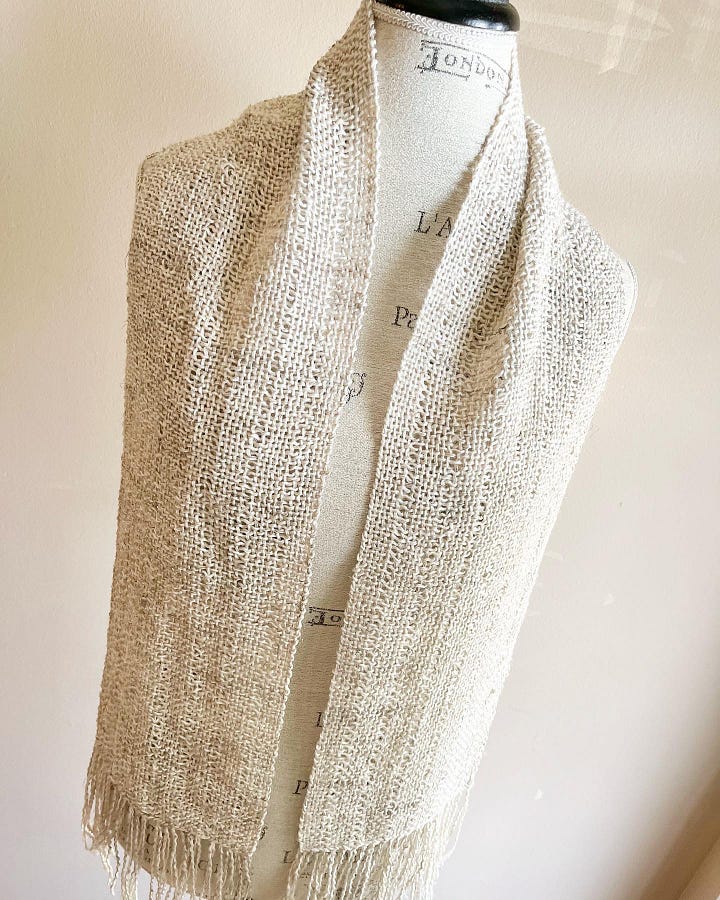

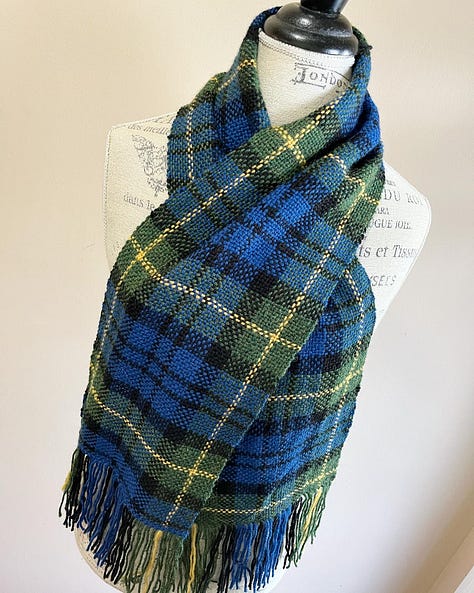
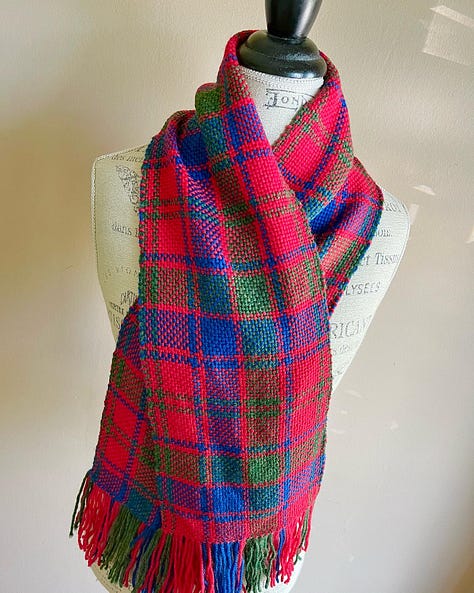
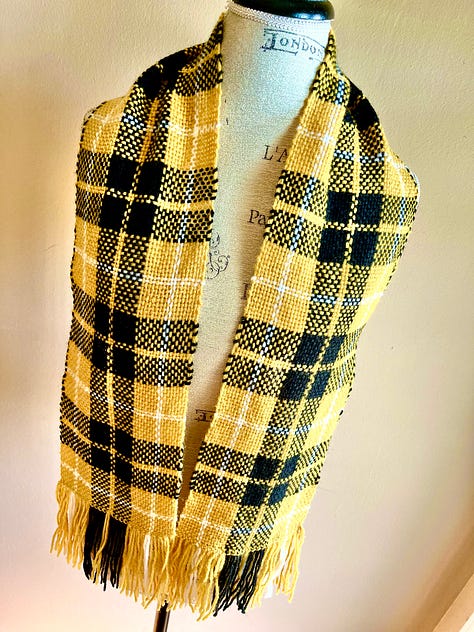
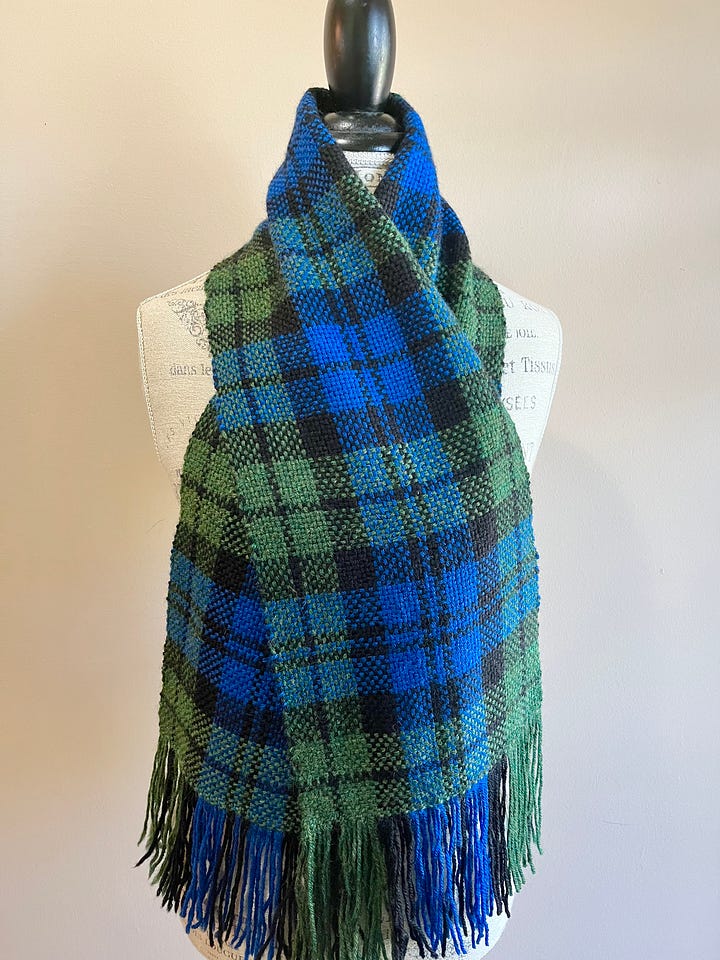
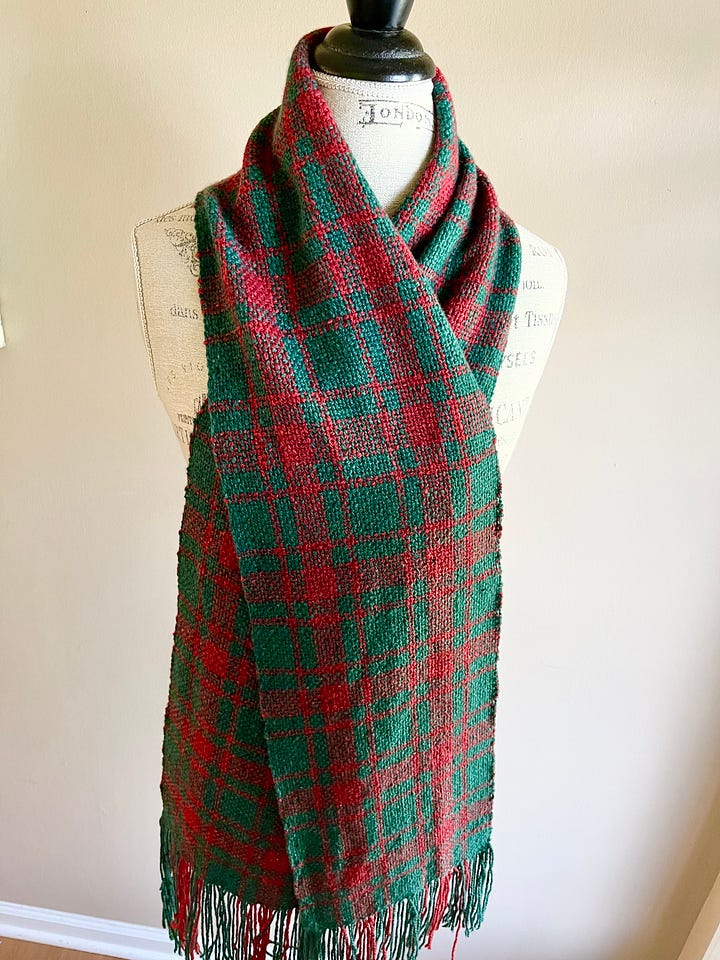
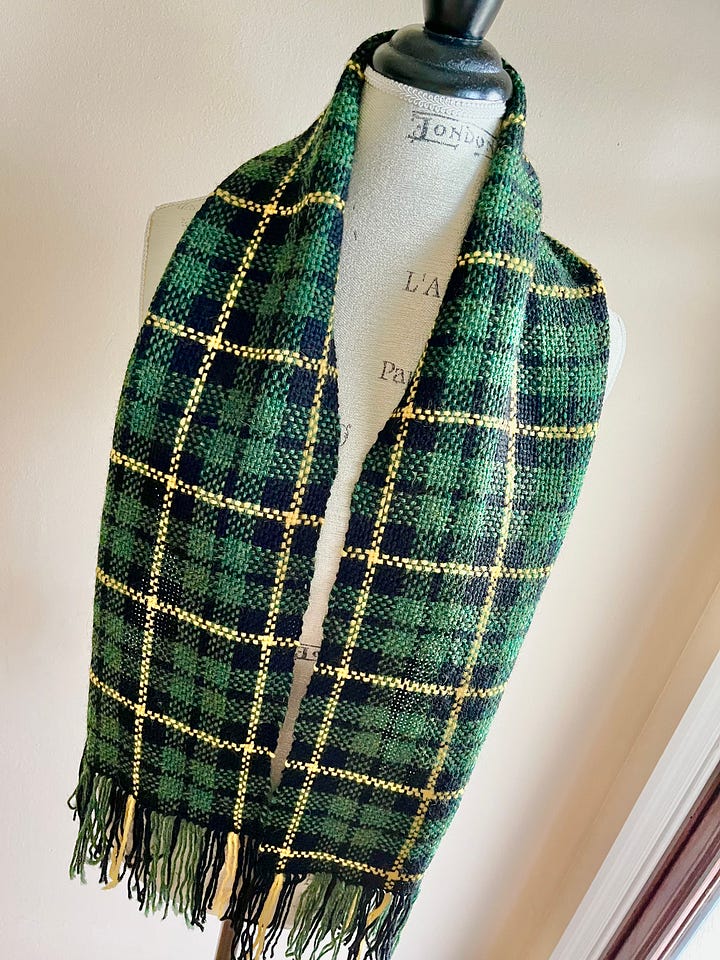
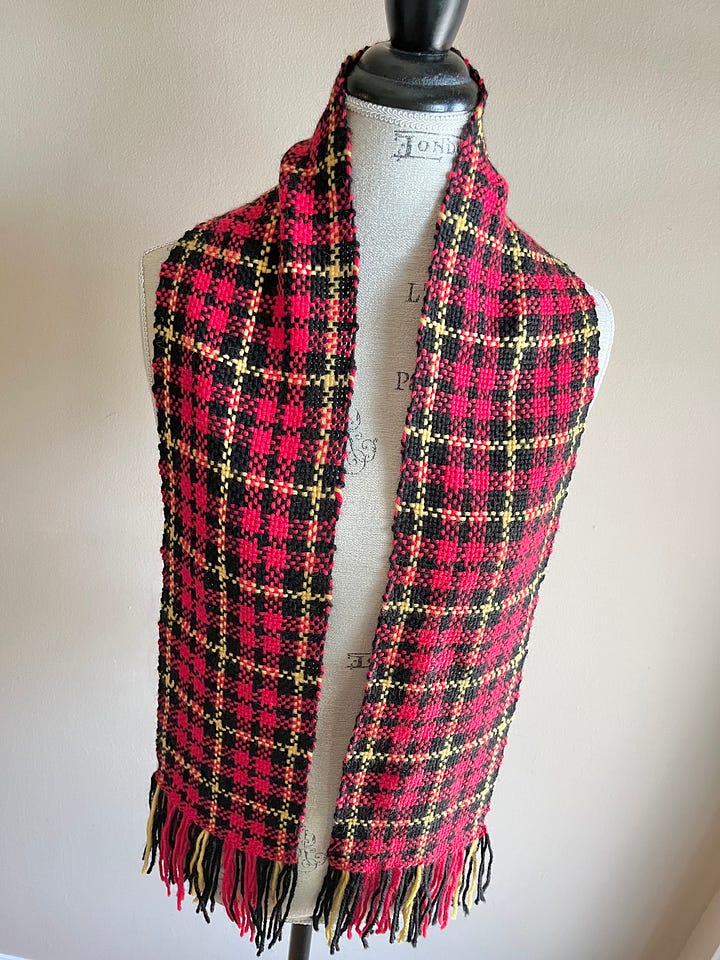
I finally managed to get enough of “Suess” (Shetland) washed fleece carded and spun into a sample skein last week. I loved it so much that I bought three more Shetland fleeces from the same farm (Ballyhoo Fiber Emporium)—two of the fleeces are from family members of Seuss (grandmother and daughter). I said I would stop buying fleeces this year until I worked through the ones I have—but it seems that last week was the week to break promises, so I just went with it.
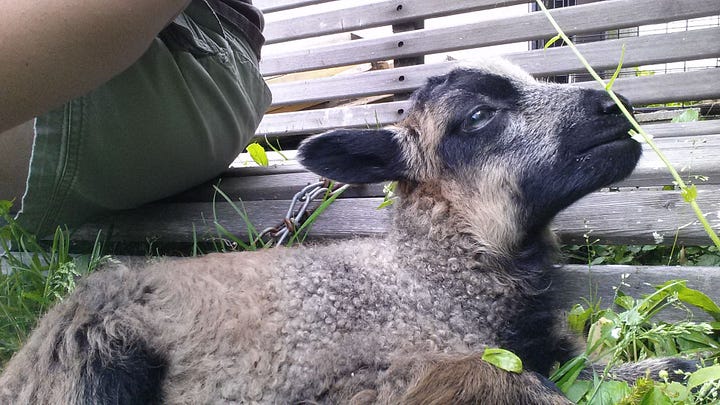
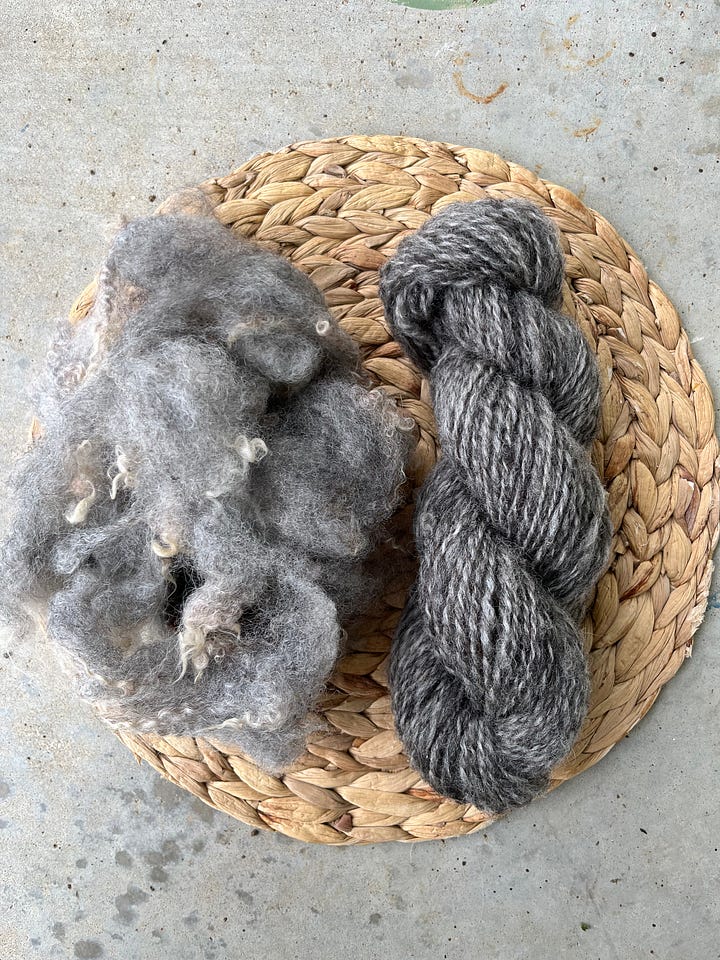
This coming Saturday, I’ll be at Pond Spring: The General Joe Wheeler Home for a weaving/spinning demo, so I’m prepping for that event this week—including building some rope/PVC pipe ladders to hang scarves from. I normally use heavy wood ladders that my husband built, but they weren’t made for outdoors, so we decided to make some display ladders that could hang from the frame of the tent instead. (I usually don’t vend at outdoor events, so it hasn’t really been an issue before now.)
Click the photo below to read more about the Joe Wheeler Home.
Those scarves are awesome.
Beautiful scarves! Congratulations on the new loom. I hope you will love it and it sounds like you do!